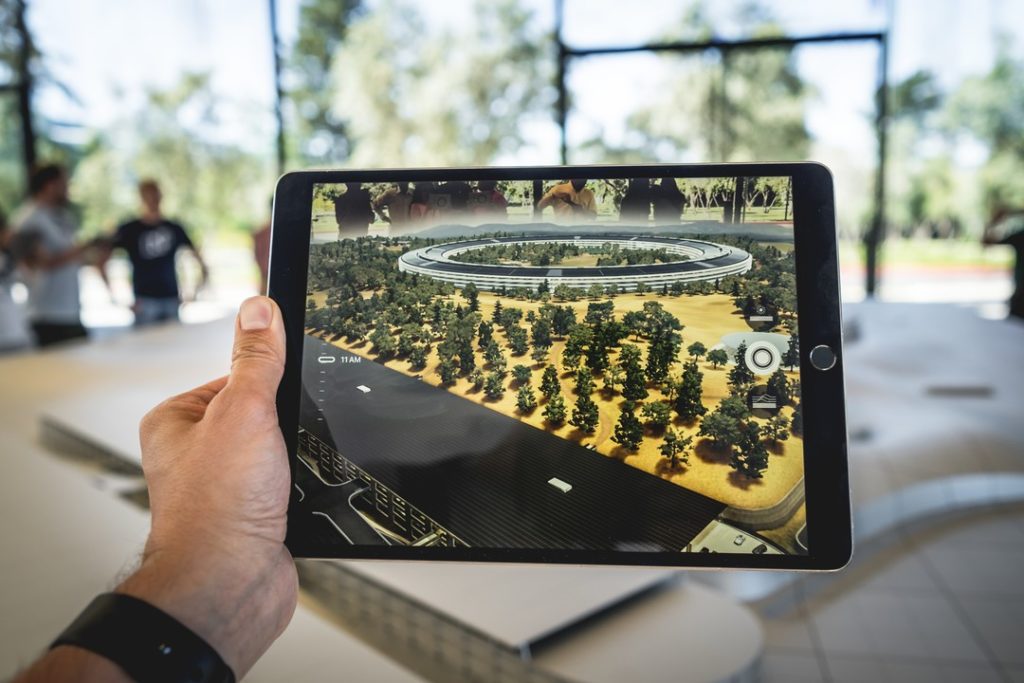
The challenge to keep and retain skilled workers is hardly new, but the skills gap has been accelerating in recent years. By 2025, analysts anticipate over 2,000,000 skilled manufacturing jobs will go unfilled. Compare that to 600,000 unfilled jobs in 2011.
Many fields are experiencing a shortage of professionals—particularly those with career- spanning expertise. Within industrial markets, there are several job functions across the value chain that are most affected, including:
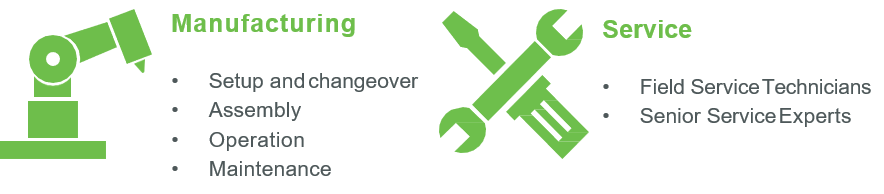
There are three methods that companies employ to maintain their reservoir of skilled expertise:
- Slowing the skills drain. By 2022, over 26% of manufacturing workers will be over 55. Age-based attrition is inevitable and difficult to address, but organizations can focus on extending career length, even if only for a few years.
- Maximizing current skil. Companies can also focus on methods to amplify the effectiveness and efficiency of their current skilled workforce. This requires organizations to enable existing experts to do more, without increasing their workload—particularly as these experts approach retirement.
- Refilling the skills reservoir. Long-term solutions require replenishing the reservoir of skills. 26.4% of field service technicians are contracted, but third-party solutions can be expensive, while negatively impacting customer satisfaction. Recruitment and in-house skills development yield better results, but come with a longer time-to-value.
As assets become increasingly customizable and are utilized across a global value chain, methods to ensure competency and mastery become both more expensive and less effective. From printed manuals and training classes, to delivering experts on site, traditional methods provide diminishing returns. Meanwhile, industrial augmented reality is quickly proving more effective.
What is industrial augmented reality?
AR technology provides users with a way to perceive and use previously hidden or inaccessible information about their environments.

Thus augmenting reality with useful, contextual data. AR is consumed via hardware, (such as a tablet, smartphone or purpose-built AR wearables), to overlay digital information on top of physical assets and environments. AR software, recognizes the physical asset, and “locks” the digital information in a way that allows users to interact with the asset information three-dimensionally and hands-free.
While AR experiences are highly customizable and evolving, three main application types have emerged as highly effective at closing the skills gap:
Product visualization
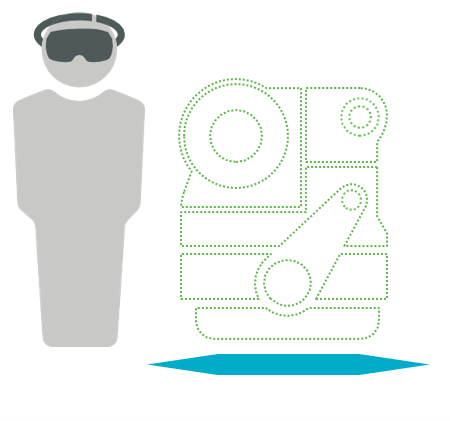
AR product visualization applications utilize augmented overlays of information, and can even provide interactive digital twins of the physical assets themselves. Product visualization is used for both training and guidance. AR can replace traditional training labs or simulations. It can also reduce risk if training involves working in hazardous environments.
Procedural guidance
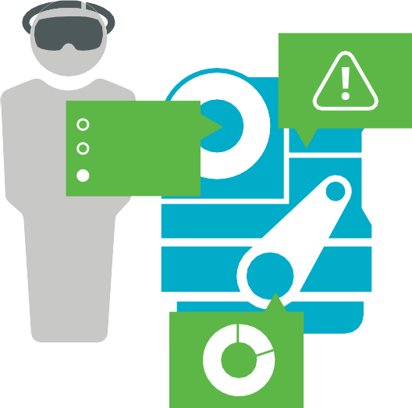
Procedural guidance utilizes the overlay of AR instructions, equipment status, or performance data atop physical assets in the workplace. This benefits workers across the experience/skill spectrum and is more focused on serving as a reference for either highly complex, customizable, or frequently changing assets.
Remote assistance
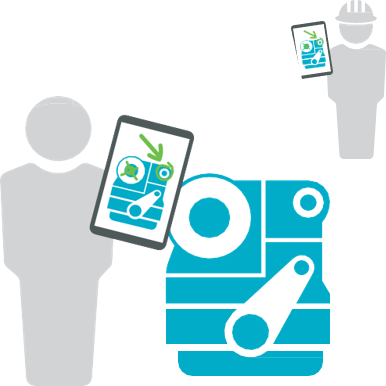
Remote assistance virtually connects experts and workers around a specific piece of equipment.
Typically combining attributes of AR and video- chat with annotations from a remote expert, a shared-view of the work environment can be a highly effective, visual medium for collaboration and problem solving.
Augmented reality is proving to be highly effective at all three strategies for closing the industrial skills gap:
Using AR to slow the skills drain:
- Remote assistance apps allow experts to share expertise, without physically having to travel on-site. This reduces the burden on senior experts, while retaining them longer as “virtual gurus.”
- As experts reach retirement age, they can provide consulting on AR experiences using product visualization and procedural guidance. This turns their individual expertise into a shareable skills resource.
Using AR to amplify current skills
- Remote assistance reduces the cost of providing highly skilled support. By lowering costs, companies can direct skilled resources to help smaller, more remote customers.
- Procedural guidance provides workers with nstruction, equipment status, and performance data while they’re working. Newer workers can become effective in the field faster, with reduced risk of novice errors. It also benefits workers of all skill levels with step-by-step depictions of equipment and process customization.
Using AR to refuel the skills tank:
- Product visualization has proven to build skills faster—from competency to mastery. Workers using AR learn faster, with improved retention.
- Coordination between production visualization-centric training, and on-the-job procedural guidance can further accelerate skills growth.
- Remote assistance can pair experts with newer workers more easily, allowing gurus to virtually act as mentors to junior workers
Industrial organizations are acutely aware of the growing skills crisis; market leaders are increasingly embracing AR as a way of preserving skills and staying ahead of the competition. If you’re interested in learning more about the role that AR can play at your organization, or how to get started building your own low-risk, high-reward AR solution, you’ll find these resources useful.